常见问题
双金属复合耐磨弯头研究生产
更新时间 2021-04-14 18:28 阅读
煤粉输送管 道是火电厂 运营过程中 的关键配 件,煤粉的输送是一个快速而持续的过程,较快的 输送速度使管道承受严重的冲击磨 损, 在弯头部 位经常发生穿洞失效现象, 使用寿 命仅为直管 的 1/3,频繁的维 修补焊已 成 为 影 响 煤 粉 输 送 效 率 的 重 要 因 素 之 一 [1]。 目前 , 电 厂 使 用 的 弯 头 多 为 16Mn 单一 材 质,硬 度 低,耐 磨 性 能 差。 单 位 承 接 某 电 厂 大 型 弯 头,金 属 焊 接 制 成,其 形 状 如 图 1。 为提高弯头的使用寿命, 将单一材质 改为双金属 复 合 弯 头,弯 头 尺 寸 较 大,为 保 证 其 品 质,采 用 消 失模铸造工艺[2]。
1 试验方法
复合弯头外壁非工作层采用钢管分节对接,内 部工作层模型由手工电阻丝切割聚苯乙烯泡沫 而 成,涂刷水基石英粉专用耐火涂料,在烘干室内进行干燥,选用底抽式真空砂箱;砂箱于二维振动台进 行震动;采用中频感应炉熔炼高铬铸铁,浇注前,开 启抽真空系统,铁液出炉温度为 1 480 ℃,浇注温度控制在 1 420~1 430 ℃,热处理在台车式电阻炉内 进行, 耐磨性试验在 NUS-IS03 型磨粒磨损试验机 上进行。
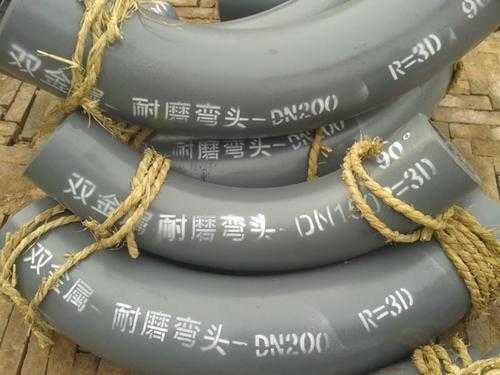
2 试制过程与结果分析
2.1 弯头材质成分选择
输送煤粉过程中,弯头部位承受煤粉的冲击与 磨损严重,因此要求弯头具备很好的耐磨性,同时, 弯头的安装、拆卸、以及使用过程中的维修都要求 其具有良好的焊接性能。 在电厂工况下,高铬铸铁 的抗磨损性能是最好的[1],但脆性很高,若单一使用 高铬铸铁材质,弯头不能焊接。使用 16Mn 材质钢管 与之复合铸造, 不仅使弯头具备了良好的耐磨性 能,而且实现了焊接,很大程度提升了弯头的使用 周期。
试 验 弯 头 工 作 层 高 铬 铸 铁 各 元 素 含 量 根 据 GB/T8263-2010 中 BTMCr15 选定 w 为:2.0%~3.6% C;≤1.2%Si;2.0%Mn;14%~18%Cr;≤3.0%Mo;≤ 2.5%Ni;Cu≤1.2%;≤0.06%P;≤0.06%S。 弯头外层 非工作层选用 16Mn 材质钢管。
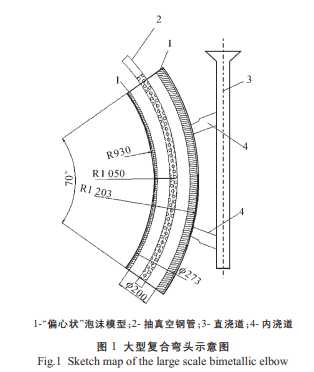
2.2 复合弯头非工作部位制作工艺
所研 制 的 弯 头 外 型 尺 寸 如 图 1,中心 弧 长 为 1 282 mm,对应的半径为 R1 050 mm,弯头 两端所 成中心角为 70°;采购成品 16Mn 材质钢管,钢管外 径为 准273 mm,壁厚 6 mm,用线切割的方法,将钢 管根据所试制弯头的角度切分为 7 段, 并按 1∶1 放 大样进行焊接,形成弯头的非工作部位。
2.3 工作部位模型制作工艺
工业发达国 家在开发消 失模铸造工 艺的过程 中,重点对大型铸件泡沫模型的热解特性,金属充 型凝固特性, 干砂充填紧实度等专题进行研究,并 取得了很好效果[3~6]。 因所制弯头尺寸较大,故内部 工作部位采用消失模铸造工艺制备。
煤粉在输送过程中,弯头背部所受的冲击磨损 最严重,所以内部工作层设计采用沿弧逐渐加厚的 “偏心”结构,如图 1 中 1 所示;弯头内部工作层“偏 心”状模型的制作选用聚苯乙烯泡沫,采用电阻丝 手工切割, 铸造收缩率为 1%。 将泡沫模型分节切 割,填充于钢管弯头内,并尽量做到严丝合缝,有缝 隙之处用报纸粘贴严实,填堵完成后涂刷镁砂粉涂 料,涂层厚度约 2.0~2.5 mm。 因弯头尺寸较大,为防 止塌箱,涂料涂刷 4 遍,每层涂刷后在烘干室内进 行烘干,待完全干燥后涂刷下一层。
2.4 浇注系统设计
由于弯头尺寸较大,采用水平式浇注易发生塌箱事故。经试验,浇注工艺采用如图 1 中的竖立式阶 梯浇注[7]。 阶梯浇注系统分 2 层浇道,两个内浇道 向同一方向倾斜;便于补缩、同时防止铁液冷却收缩 将其拉裂。 根据文献介绍[8],阶梯式浇注系统的直 浇道 截面积应大于其他浇道截面积, 研制试验设 计直浇道截面尺寸 45 mm×45 mm,内浇道截面尺寸 30 mm×45 mm,长 180 mm。
2.5 模型合箱
弯头内涂料完全干透后, 将模型与浇注系统组 装 完整,同时在 弯 头 内 设 置 抽 真 空 钢 管,图 1 中 2 所示。 之前试制过程中因没设抽真空钢管, 发生胀箱 和塌箱现象,致铸件不合格,经分析讨论其原因为: 弯头内腔型砂紧密度和硬度不够。 弯头内部设置抽 真空钢管可增强型砂硬度和紧密度, 有效防止胀箱 等现象发生。
抽真空钢管固定于弯头内中心位置, 避免偏心 与内壁接触,防止抽塌。将组装好的模型整体放入砂 箱内,检查涂料有无脱落或“露白”现象,若有发生及 时用泥粘严,避免浇注时型砂进入铸件形成夹砂。 砂箱内以硅砂作为型砂, 模型在砂箱内的吃砂 量 为:下 部 90~100 mm,四壁 与 上 部 120~150 mm。 将砂箱置于二维震动台震动 1 min 左右, 后吊入浇 注坑。 表面覆盖塑料薄膜,放置浇口杯,将潮砂覆于 薄膜上, 用于固定浇口杯以及防止外溅铁液烧破薄 膜而泄压。
2.6 铁液熔炼与浇注
高 铬 铸 铁 的 熔 炼 在 250 kg 中 频 感 应 炉 内 进 行,按照已设定铁液的化学成分进行配料计算。 装 炉时炉料要紧密,以求快速熔化;开始通电 6~8 min 内先以小功率送电,待电流冲击停止 后,逐渐将功 率 增 至 最 大 ; 熔 炼 过 程 中 应 随 时 推 料 防 止 “搭 桥 ” ,并 陆 续 添 加 炉 料。 待 炉 料 全 部 熔 化,温 度 升 至 1 480 ℃时出 铁 液, 并 开 启 真 空 泵, 铁 液 镇 静 2~3 min 后进行浇注。浇注完成后将负压度调整为 -0.025 MPa,抽真空保持 15 min 关闭真空泵,铸件 于砂箱内保温 8 h 倒箱。 铸件在空气中冷却。
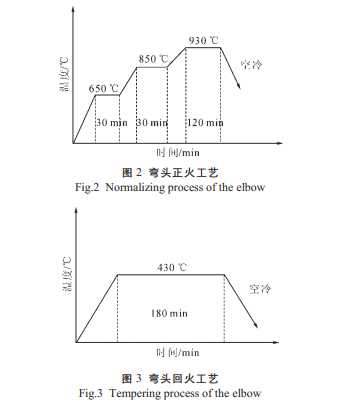
2.7 热处理工艺
为了提高大型复合弯头使用寿命, 达到火力发 电厂输送煤粉的指标要求, 对弯头进行了正火和回 火处理。 正火和回火工艺如图 2 和图 3 所示。
2.8 耐磨性试验及结果分析
为对比双金属弯头与单一材质 16Mn 弯头的耐 磨损性能, 分别从研制成功的双金属弯头及 16Mn 弯头上取样,进行了磨粒磨损试验。将 试样 制 成 50 mm×50 mm×4 mm 的试 样 块, 于 NUS-ISO3 型磨粒磨损试验机上进行磨损试验, 记 录 试 样 减 重 量;对 试 验 机“往 复 次 数”及 试 样 块 “累计减重量” 用的函数关系 Origin 软件进行直线 拟合,分别得到如图 4 所示的两条直线,直线斜率 即表示试样的磨损率。
从图 4 中直线 斜率可以得 出: 双 金 属 弯 头 试 样 的 耐 磨 性 能 是 16Mn 材 质 弯 头 耐 磨 性 能 的 2.05倍。
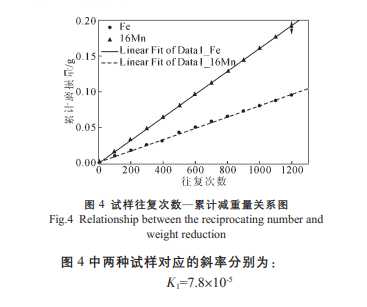
2.9 大型双金属弯头的应用
研制成功的大型复合弯头在某电厂进行了装机 试验,现场跟踪表明:使用了 18 个月未发现穿孔失 效现象, 较该电厂原配弯头使用寿命提高 2~3 倍, 品质得到该电厂的认可。
3 结论
(1)采用消失模固液复合铸造 16Mn 材质钢-高 铬铸铁复合大型弯头, 既保证了弯头良好的焊接性 能,同时拥有很高的耐磨性,大幅度增加了弯头的使 用周期,提高了煤粉输送效率。
(2)(2)浇注 过 程 中,采 用 竖 立 式 阶 梯 浇 注 并 在 复 合 弯头内添加抽真空钢管,有效解决了塌 箱、胀箱 问题。
(3)(3)与单一材质 16Mn 弯头相比,双金属复合弯 头的耐磨性能是其 2.05 倍, 使用寿命较前者提高 2~3 倍。
1 试验方法
复合弯头外壁非工作层采用钢管分节对接,内 部工作层模型由手工电阻丝切割聚苯乙烯泡沫 而 成,涂刷水基石英粉专用耐火涂料,在烘干室内进行干燥,选用底抽式真空砂箱;砂箱于二维振动台进 行震动;采用中频感应炉熔炼高铬铸铁,浇注前,开 启抽真空系统,铁液出炉温度为 1 480 ℃,浇注温度控制在 1 420~1 430 ℃,热处理在台车式电阻炉内 进行, 耐磨性试验在 NUS-IS03 型磨粒磨损试验机 上进行。
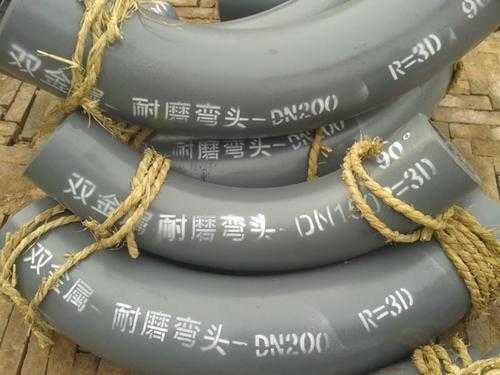
2 试制过程与结果分析
2.1 弯头材质成分选择
输送煤粉过程中,弯头部位承受煤粉的冲击与 磨损严重,因此要求弯头具备很好的耐磨性,同时, 弯头的安装、拆卸、以及使用过程中的维修都要求 其具有良好的焊接性能。 在电厂工况下,高铬铸铁 的抗磨损性能是最好的[1],但脆性很高,若单一使用 高铬铸铁材质,弯头不能焊接。使用 16Mn 材质钢管 与之复合铸造, 不仅使弯头具备了良好的耐磨性 能,而且实现了焊接,很大程度提升了弯头的使用 周期。
试 验 弯 头 工 作 层 高 铬 铸 铁 各 元 素 含 量 根 据 GB/T8263-2010 中 BTMCr15 选定 w 为:2.0%~3.6% C;≤1.2%Si;2.0%Mn;14%~18%Cr;≤3.0%Mo;≤ 2.5%Ni;Cu≤1.2%;≤0.06%P;≤0.06%S。 弯头外层 非工作层选用 16Mn 材质钢管。
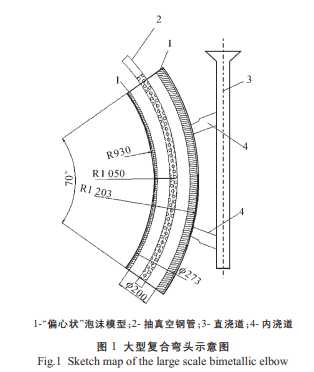
2.2 复合弯头非工作部位制作工艺
所研 制 的 弯 头 外 型 尺 寸 如 图 1,中心 弧 长 为 1 282 mm,对应的半径为 R1 050 mm,弯头 两端所 成中心角为 70°;采购成品 16Mn 材质钢管,钢管外 径为 准273 mm,壁厚 6 mm,用线切割的方法,将钢 管根据所试制弯头的角度切分为 7 段, 并按 1∶1 放 大样进行焊接,形成弯头的非工作部位。
2.3 工作部位模型制作工艺
工业发达国 家在开发消 失模铸造工 艺的过程 中,重点对大型铸件泡沫模型的热解特性,金属充 型凝固特性, 干砂充填紧实度等专题进行研究,并 取得了很好效果[3~6]。 因所制弯头尺寸较大,故内部 工作部位采用消失模铸造工艺制备。
煤粉在输送过程中,弯头背部所受的冲击磨损 最严重,所以内部工作层设计采用沿弧逐渐加厚的 “偏心”结构,如图 1 中 1 所示;弯头内部工作层“偏 心”状模型的制作选用聚苯乙烯泡沫,采用电阻丝 手工切割, 铸造收缩率为 1%。 将泡沫模型分节切 割,填充于钢管弯头内,并尽量做到严丝合缝,有缝 隙之处用报纸粘贴严实,填堵完成后涂刷镁砂粉涂 料,涂层厚度约 2.0~2.5 mm。 因弯头尺寸较大,为防 止塌箱,涂料涂刷 4 遍,每层涂刷后在烘干室内进 行烘干,待完全干燥后涂刷下一层。
2.4 浇注系统设计
由于弯头尺寸较大,采用水平式浇注易发生塌箱事故。经试验,浇注工艺采用如图 1 中的竖立式阶 梯浇注[7]。 阶梯浇注系统分 2 层浇道,两个内浇道 向同一方向倾斜;便于补缩、同时防止铁液冷却收缩 将其拉裂。 根据文献介绍[8],阶梯式浇注系统的直 浇道 截面积应大于其他浇道截面积, 研制试验设 计直浇道截面尺寸 45 mm×45 mm,内浇道截面尺寸 30 mm×45 mm,长 180 mm。
2.5 模型合箱
弯头内涂料完全干透后, 将模型与浇注系统组 装 完整,同时在 弯 头 内 设 置 抽 真 空 钢 管,图 1 中 2 所示。 之前试制过程中因没设抽真空钢管, 发生胀箱 和塌箱现象,致铸件不合格,经分析讨论其原因为: 弯头内腔型砂紧密度和硬度不够。 弯头内部设置抽 真空钢管可增强型砂硬度和紧密度, 有效防止胀箱 等现象发生。
抽真空钢管固定于弯头内中心位置, 避免偏心 与内壁接触,防止抽塌。将组装好的模型整体放入砂 箱内,检查涂料有无脱落或“露白”现象,若有发生及 时用泥粘严,避免浇注时型砂进入铸件形成夹砂。 砂箱内以硅砂作为型砂, 模型在砂箱内的吃砂 量 为:下 部 90~100 mm,四壁 与 上 部 120~150 mm。 将砂箱置于二维震动台震动 1 min 左右, 后吊入浇 注坑。 表面覆盖塑料薄膜,放置浇口杯,将潮砂覆于 薄膜上, 用于固定浇口杯以及防止外溅铁液烧破薄 膜而泄压。
2.6 铁液熔炼与浇注
高 铬 铸 铁 的 熔 炼 在 250 kg 中 频 感 应 炉 内 进 行,按照已设定铁液的化学成分进行配料计算。 装 炉时炉料要紧密,以求快速熔化;开始通电 6~8 min 内先以小功率送电,待电流冲击停止 后,逐渐将功 率 增 至 最 大 ; 熔 炼 过 程 中 应 随 时 推 料 防 止 “搭 桥 ” ,并 陆 续 添 加 炉 料。 待 炉 料 全 部 熔 化,温 度 升 至 1 480 ℃时出 铁 液, 并 开 启 真 空 泵, 铁 液 镇 静 2~3 min 后进行浇注。浇注完成后将负压度调整为 -0.025 MPa,抽真空保持 15 min 关闭真空泵,铸件 于砂箱内保温 8 h 倒箱。 铸件在空气中冷却。
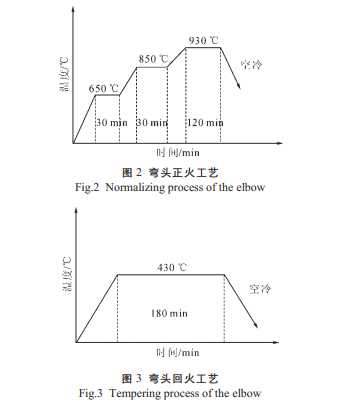
2.7 热处理工艺
为了提高大型复合弯头使用寿命, 达到火力发 电厂输送煤粉的指标要求, 对弯头进行了正火和回 火处理。 正火和回火工艺如图 2 和图 3 所示。
2.8 耐磨性试验及结果分析
为对比双金属弯头与单一材质 16Mn 弯头的耐 磨损性能, 分别从研制成功的双金属弯头及 16Mn 弯头上取样,进行了磨粒磨损试验。将 试样 制 成 50 mm×50 mm×4 mm 的试 样 块, 于 NUS-ISO3 型磨粒磨损试验机上进行磨损试验, 记 录 试 样 减 重 量;对 试 验 机“往 复 次 数”及 试 样 块 “累计减重量” 用的函数关系 Origin 软件进行直线 拟合,分别得到如图 4 所示的两条直线,直线斜率 即表示试样的磨损率。
从图 4 中直线 斜率可以得 出: 双 金 属 弯 头 试 样 的 耐 磨 性 能 是 16Mn 材 质 弯 头 耐 磨 性 能 的 2.05倍。
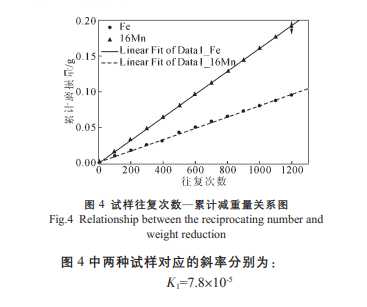
2.9 大型双金属弯头的应用
研制成功的大型复合弯头在某电厂进行了装机 试验,现场跟踪表明:使用了 18 个月未发现穿孔失 效现象, 较该电厂原配弯头使用寿命提高 2~3 倍, 品质得到该电厂的认可。
3 结论
(1)采用消失模固液复合铸造 16Mn 材质钢-高 铬铸铁复合大型弯头, 既保证了弯头良好的焊接性 能,同时拥有很高的耐磨性,大幅度增加了弯头的使 用周期,提高了煤粉输送效率。
(2)(2)浇注 过 程 中,采 用 竖 立 式 阶 梯 浇 注 并 在 复 合 弯头内添加抽真空钢管,有效解决了塌 箱、胀箱 问题。
(3)(3)与单一材质 16Mn 弯头相比,双金属复合弯 头的耐磨性能是其 2.05 倍, 使用寿命较前者提高 2~3 倍。
- 上一篇:不锈钢法兰,弯管精密,铸造技术
- 下一篇:碳钢和不锈钢法兰连接的腐蚀问题及解决方案